A complete Technological Offer whatever your needs are!
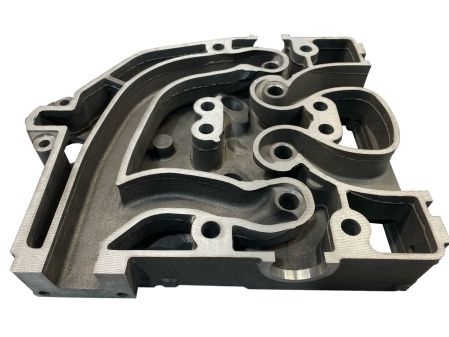
Fiday Gestion has developed a technology in the Lost Foam lamellar gray cast iron, a process in which from a model in expanded polystyrene of the part will be coated. Then, a dry and fluid sand will be injected and vibrated, which will allow to keep the model in place before the casting of the iron which will take the place of the polystyrene.
Thanks to this process Fiday Gestion obtains an optimal quality to realize parts with very complex shapes without cores with a minimum of finishing and this while respecting the environment!
Our grey iron technology is unique in Europe!
LOST FOAM
Fiday gestion has decided to invest in the Lost Foam production technology to guarantee a complete range of products at a very competitive price!
After several years of development Fiday Gestion has acquired a unique expertise on this process, a workforce that has now increased fivefold! Our site is able to produce 40 000 caissons per year with a capacity per crate from 1 to 300kg of grey lamellar iron. We are the only company in Europe to use this process with lamellar grey iron.
What are the steps of the process ?
First of all, we receive polystyrene models from several partners who are experts in this field, to which we add a bonding casting system.
The polystyrenes are all checked before the coating phase in a bath made of refractory inorganic materials and then placed in an oven at 55°C where the polystyrenes will spend a total of 6 hours.
Then comes the vibration molding which is done with a dry and fluid sand that will keep the part in place during the casting.
During the source casting, the vacuum is created in the box and the cast iron will take the place of the polystyrene.
Afterwards, the parts are sent to shot blasting and finishing for final checks such as ultrasonic checks, high pressure leakage tests and other verification tests according to the customers' specifications.
After these last actions the parts are stored in their final packaging.
What are the advantages of Lost Foam ?
The advantages of Lost Foam are multiple:
- 0 core
- Easy to finish
- Thinness of thickness (up to 5 mm)
- Weight and time saving / machining operations
Lost Foam can allow you to reduce the number of sub-assemblies and to make a single part where you had a set of several mechanically welded parts for example. The applications are multiple and require rethinking the function of the parts to optimize costs.
Environmentally, Lost Foam uses no binders and no chemicals.
Polystyrene burns and creates water with hydrogen. Unlike a traditional green sand site, 100% of the sand is recycled after passing through a closed hydraulic circuit cooler.